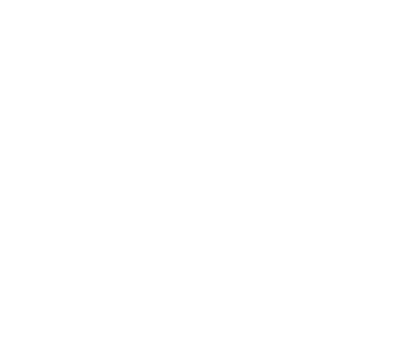

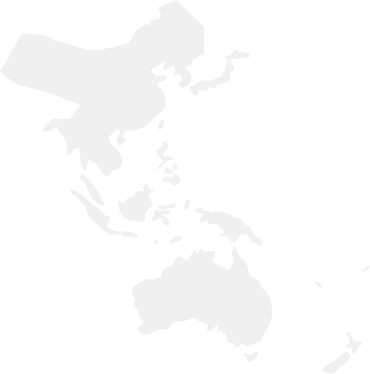
VeoVa Vinyl Esters are co-monomers in emulsion polymers for high quality, interior paints and coatings, in addition to other applications....
Hexion supplies a range of resin systems and monomers for manufacturing coatings used in industrial, masonry and other applications....
Hexion offers a complete line of binding resins for all varieties of particleboard and fiberboard....
Hexion is a leading global supplier of formaldehyde for wood and industrial resins....
Wood coatings made with emulsions based on VeoVa monomers enhance long term outdoor durability....
At Hexion, Sustainability is an integrated business approach that creates long-term stakeholder value....
Get compliant with this economical dust suppressant that traps fine dust particles and remains on the proppant during transportation and transfer....
Here are the stories of how we leverage the power of chemistry and enabling technologies to deliver more sustainable solutions that make this world better, safer and cleaner....
Hexion offers effective fluid loss additives, cement antifoams, and formation fines control agents....
Hexion ArmorBuilt Wildfire Shield protects wood utility poles against the damaging effects of wildfires....
Hexion recently joined the U.S. Environmental Protection Agency’s (EPA’s) ENERGY STAR program as a partner....